Author: Anuj Narang
A plant’s profitability can be significantly increased by improving control and maximizing the production of its highest-value products. Most natural gas producers in Canada also remove the heavier hydrocarbon liquids from the natural gas stream. These heavier hydrocarbon liquids also referred to as Natural Gas Liquids (NGLs) include ethane (C2), propane (C3), butanes (C4), and condensate (C5+). Recovery of NGL components in gas not only helps with hydrocarbon dew point control in a natural gas stream but also yields a source of revenue, as NGLs normally have significantly greater value as separate marketable products than as part of the natural gas stream. Lighter NGL fractions, such as ethane, propane, and butanes, can be sold as fuel or feedstock to refineries and petrochemical plants, while the heavier portion can be used as a blending with gasoline.
Maximizing the recovery of NGLs from natural gas can improve margins tremendously for gas plants. Optimizing recovery of NGLs and increasing product yields is imperative for gas producers to sustain and profit in the competitive natural gas market. The Natural Gas Liquid Recovery and Condensate Stabilizer Units are the primary areas of a Natural Gas Plant which have the highest impact on the gross profit for a facility.
Maximizing the recovery of NGLs from natural gas can improve margins tremendously for gas plants. Optimizing recovery of NGLs and increasing product yields is imperative for gas producers to sustain and profit in the competitive natural gas market. The Natural Gas Liquid Recovery and Condensate Stabilizer Units are the primary areas of a Natural Gas Plant which have the highest impact on the gross profit for a facility.
Challenges
Most Shallow Cut Natural Gas Processing facilities in Canada that separate NGLs have either type A or type B fractionation units as shown in Figure 1. Deep Cut facilities also have De-methanizer upstream of De-ethanizer to recover more liquids and separate natural gas from C2-rich NGLs. The primary focus of this blog is on Shallow Cut facilities. Typically, these facilities either produce NGLs and Condensate or separate NGLs further to produce Liquefied Petroleum Gas (LPG) and additional Condensate. NGL separation is done through fractionation columns in the form of De-ethanizer, De-Butanizer, and Condensate Stabilizer units.
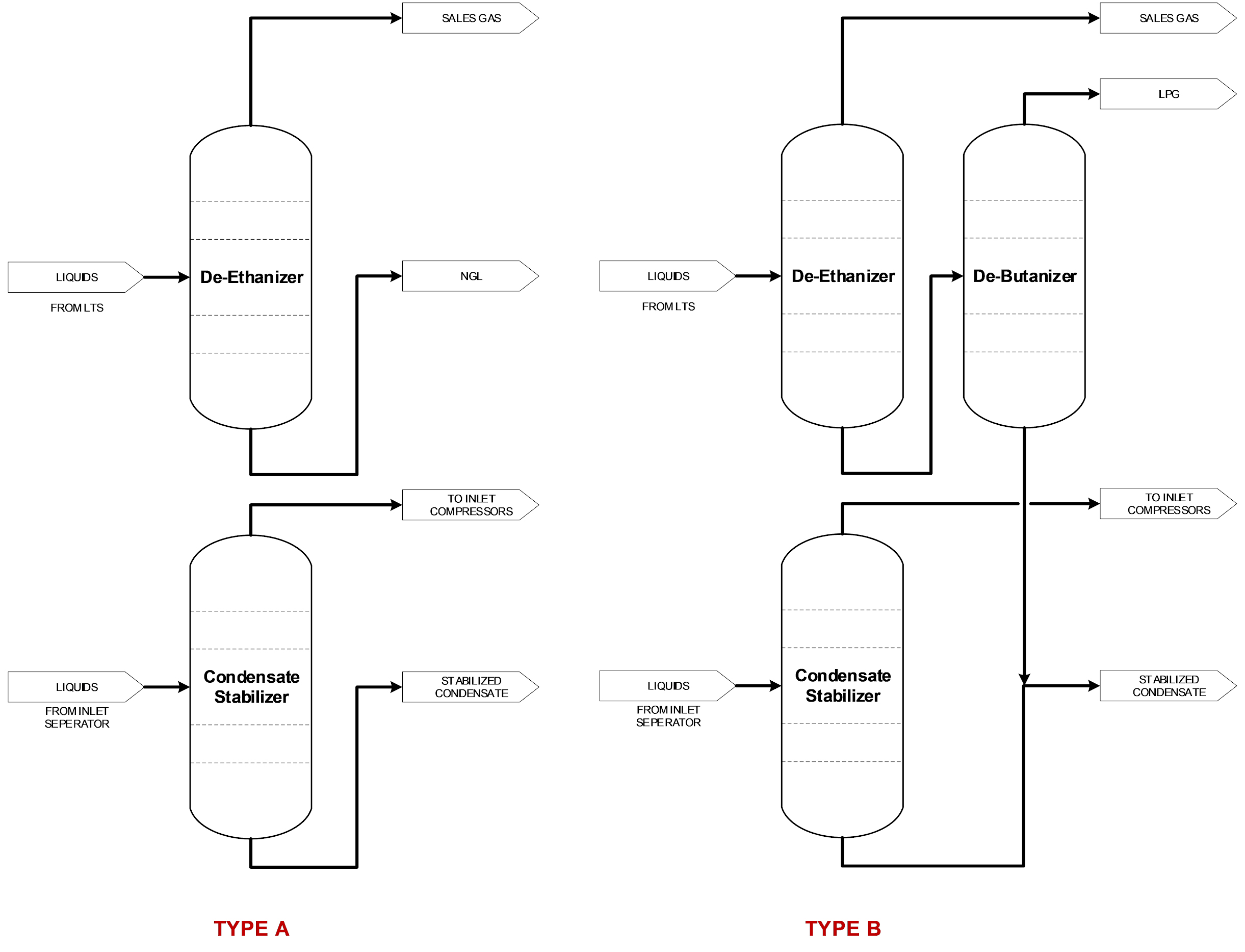
NGL Recovery Units in a Natural Gas Processing Facilities
Figure 1
Condensate produced in Canada from different gas plants is usually blended into a few streams and is transported by pipeline to the market. The pipeline shippers have developed an equalization system to account for slight differences in product qualities from individual gas plants. The equalization procedure guide determines the value of each delivery to reflect that product quality difference. Product Quality penalties or credits are determined from the density, sulphur content, and Deemed Butane (C4-) content of the condensate, and adjustments are based on monthly average composition. Deemed Butane is defined as vol% of Butane + 3 x vol% C3. Click here for more details on the equalization guidelines.
Based on November 2023 prices of NGLs in Alberta, the price differential between LPG (Butane Mix Price) and Condensate is $372 CAD/m3.and the price differential between Sales gas and LPG (Butane Mix Price) is $233 CAD/m3. Many facility operators don’t understand the real difference between product specification and product quality. Also, many facilities do not have the measurement devices required to control the product quality in real-time of the NGL products. The primary objective at these facilities is to ensure product meets the specifications of the transporter (truck or pipeline) and the buyer. These specifications for condensate are mainly for vapor pressure less than 103 kPaa, total sulphur content less than 0.5 wt%, and moisture content less than 0.5 vol%. However, the secondary but the economic objective of the Condensate Stabilizer and De-Butanizer units are to maximize yield and maximize the product quality with Deemed Butane up to 5 vol%. As a result, some of the NGL or LPG can be sold as produced condensate. The product specification for pipeline shippers on C2:C3 ratio for NGL and LPG is 6 mol% while the product quality limit on C2:C3 ratio is 2 mol% (between 2% and 6%, gets no value) where C2 in C3 up to 2% can be sold as NGL or LPG product which otherwise would have been recovered as sales gas.
Many operators treat Deemed Butane and C2:C3 ratio as a specification and try to stay away from 5 vol% and 2 mol% respectively, as much as possible. However, the best pricing scenario to maximize revenues for the Condensate is to run closer to 5 vol% and not go over 5 vol% to avoid any financial penalties and for NGL and LPG, is to have C2:C3 ratio closer to 2 mol%. Also, by maximizing the product qualities it will result in lesser energy consumption and reduced emissions which is added benefit of optimizing these units. Figure 2 shows the Deemed Butane penalty scale based on the equalization procedure guide, where if the Deemed Butane is over 5 vol%, the first 5 vol % of the Deemed Butane condensate receives Condensate price but the portion over 5 vol% receives no value.
Many operators treat Deemed Butane and C2:C3 ratio as a specification and try to stay away from 5 vol% and 2 mol% respectively, as much as possible. However, the best pricing scenario to maximize revenues for the Condensate is to run closer to 5 vol% and not go over 5 vol% to avoid any financial penalties and for NGL and LPG, is to have C2:C3 ratio closer to 2 mol%. Also, by maximizing the product qualities it will result in lesser energy consumption and reduced emissions which is added benefit of optimizing these units. Figure 2 shows the Deemed Butane penalty scale based on the equalization procedure guide, where if the Deemed Butane is over 5 vol%, the first 5 vol % of the Deemed Butane condensate receives Condensate price but the portion over 5 vol% receives no value.
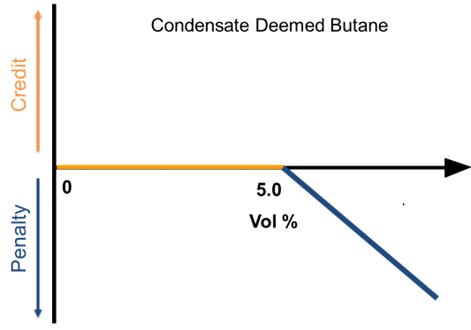
Condensate Deemed Butane Penalty Scale
Figure 2
Condensate being the most valuable product produced at the gas plant, there exists an opportunity to maximize condensate production in most gas plants by maximizing Deemed Butane up to 5 vol%. Maximizing Deemed Butane also makes the Condensate lighter and helps with the density adjustments.
Solution
Spartan recently worked with a Shallow Cut Natural gas processing facility after the gas plant started production. This facility is Type B facility and separates NGLs in the form of LPG and Condensate. Plant operations identified specific PID control loops and plant areas that were performing poorly and as a result, they would see large oscillations with a large number of alarms. The composition analysis (vol%) using NIR Spectrometers was available in real-time on the De-Butanizer LPG and Condensate as well as Stabilizer Condensate streams. C2:C3 ratio on the LPG stream and Deemed Butane contents in the condensate stream were monitored regularly but there was no direct control of these qualities. As a result of the poor performance of the base control loops, there was large variability in the Deemed Butane for Condensate and C2:C3 ratio in the LPG stream, very similar to the baseline case as shown in Figure 3.
Spartan’s Engineers performed systematic site-wide tuning where 50+ control loops were reviewed and tuned at this gas processing facility. These included the control loops in the high-value NGL fractionation and Condensate Stabilizer units. By stabilizing the base PID controls, it improved the overall stability of the plant and there was a significant reduction in variance of the product qualities, very similar to the stabilized case as shown in Figure 3. Advanced Process Control Opportunity assessment was further completed by Spartan controls to identify the opportunity post-tuning to further optimize these units using APC, resulting in higher ROI by running closer to the Deemed Butane of 5 vol% for the Condensate and C2:C3 ratio of 2 mol% for the LPG, very similar to the optimized case as shown in Figure 3.
Spartan’s Engineers performed systematic site-wide tuning where 50+ control loops were reviewed and tuned at this gas processing facility. These included the control loops in the high-value NGL fractionation and Condensate Stabilizer units. By stabilizing the base PID controls, it improved the overall stability of the plant and there was a significant reduction in variance of the product qualities, very similar to the stabilized case as shown in Figure 3. Advanced Process Control Opportunity assessment was further completed by Spartan controls to identify the opportunity post-tuning to further optimize these units using APC, resulting in higher ROI by running closer to the Deemed Butane of 5 vol% for the Condensate and C2:C3 ratio of 2 mol% for the LPG, very similar to the optimized case as shown in Figure 3.
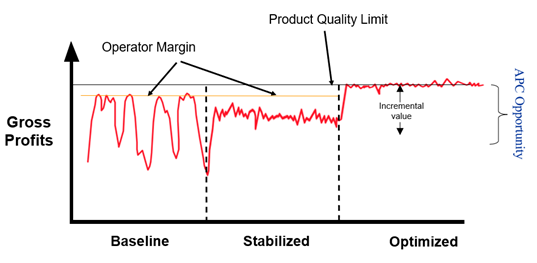
Product Quality control opportunity with APC
Figure 3
For decades, APC has proven to reduce the process variability by actively controlling key process variables and as a result the unit can operate close to the maximum possible profit day in and day out, safely and reliably. APC considers process dynamics, interactions, constraints, and economics in real-time to predict future process conditions and maintain product qualities making necessary adjustments to increase yields while reducing energy consumption. The availability of reliable and online quality measurements (from NIR spectrometer) made APC control strategy possible by providing continuous signal for feedback control.
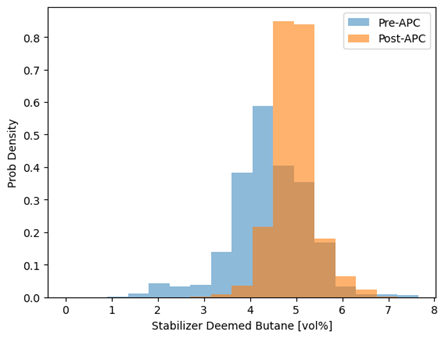
Condensate Deemed Butane control pre-APC and post-APC
Figure 4
Spartan developed and deployed APC applications for the De-Butanizer and Condensate Stabilizer units at this facility. APC pushed the mean Deemed Butane value to 4.96% with the overall variability reduction by 50% and was able to reduce operator workload significantly. Within a few months of the operation, the improvements were significant for both De-Butanizer and Condensate Stabilizer units. See Figure 4 for before and after comparison for 2 months of operations with APC. Spartan Controls also developed and historized the Business level and engineering level Key Performance Indicators (KPIs) in the DCS to assess the performance and benefits of APC in real-time.
Conclusion
Some of the major natural gas processing plants have already embarked on the digital transformation journey, leveraging predictive control and economics to measure and accurately control product quality in real-time based on profitability and optimizing the recovery of NGLs. As a result, they are reaping significant benefits from improved processing margins, allowing them to achieve the next level of operational efficiency with up to 1-2% improvement in processing margins. If you need measurement devices to control the product quality and improve product quality margins for NGLs using APC, or are interested in learning more, please contact Spartan Controls. At Spartan Controls, we invite you to “Experience Industrial Innovation”.
Learn more
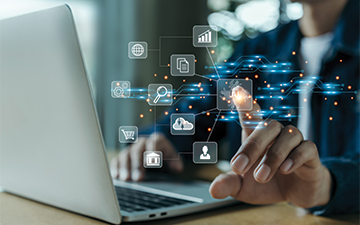