Author: Warren Mitchell
The adoption of Industry 4.0, also known as the large-scale digitalization of industrial businesses, is rapidly changing the way industrial operations are run. This digital transformation has required significant investments from operating companies and their partners in operations technology and information technology. One pillar of Industry 4.0 speaks to ubiquitous connectivity, data, and information transparency required by industry, leading to significant changes in the way industrial work is organized and performed. For industrial operations the business goals related to safety, production optimization, reliability and energy and emissions are primary targets of these programs.
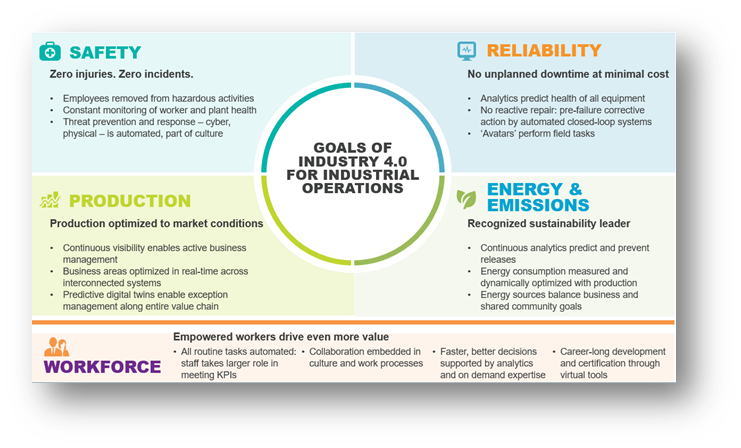
Despite these technological advancements however, many organizations with existing industrial operations continue to struggle to effectively connect their OT and IT environments in scalable ways.
Despite these technological advancements however, many organizations with existing industrial operations continue to struggle to effectively connect their OT and IT environments in scalable ways. Many continue to use legacy point connectivity solutions to connect various plant and cloud endpoints. Open Platform Communications (OPC) is a standard that was popularized in the 1990s (then referred to as OLE for Process Control) as a means of interconnecting industrial systems at the plant level. While these solutions work well for point-to-point connections, they were not originally designed for the kind of ubiquitous industrial data access that is prescribed in Industry 4.0. Each connection must be independently managed and maintained, secured, and upgraded, and as the number of data sources and applications grows, the number of connections to be managed can grow geometrically, leading to complex architectures that are difficult to troubleshoot and practically impossible to scale. Legacy OT systems and networks were never conceived or designed for the open access desired by many of these organizations.
OT network load balancing, network tunneling, and data security are examples of challenges that must be addressed for each connection to a host system. Legacy OT data plumbing issues have been one of the biggest technical barriers to the large-scale digitalization of industrial operations.
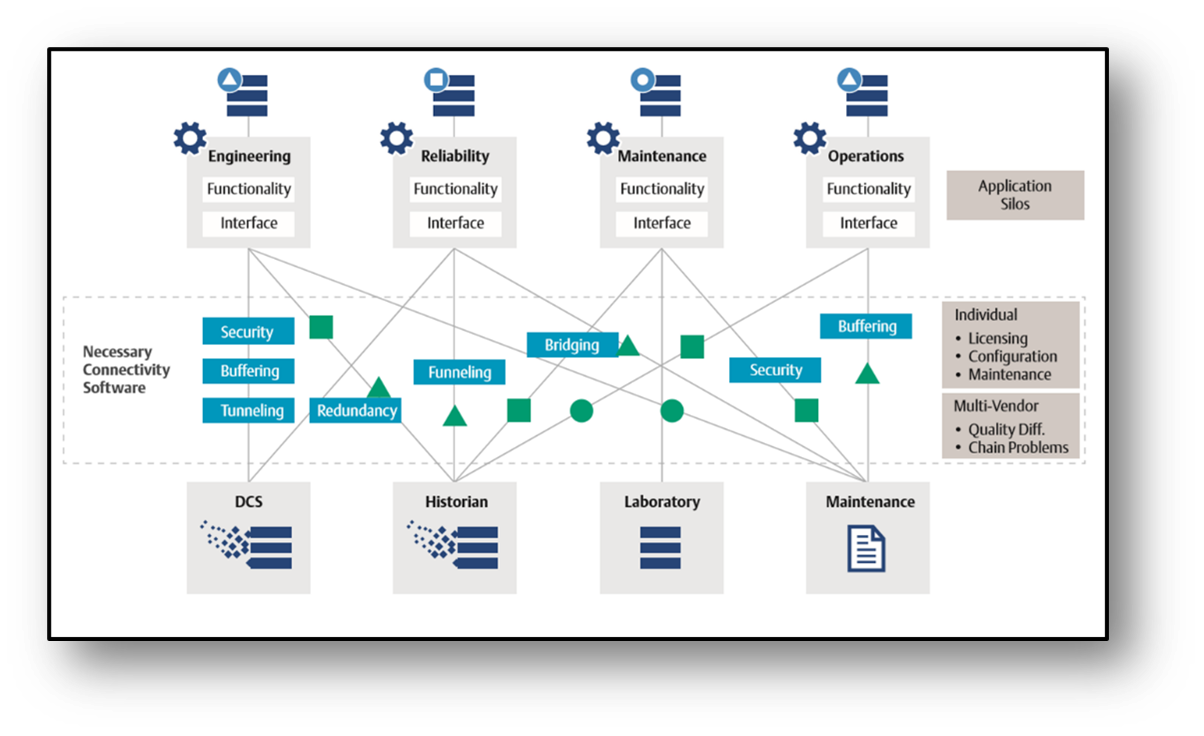
Fortunately, new scalable industrial connectivity hubs and data brokers have emerged that provide centrally managed and scalable data access between manufacturing operations and enterprise IT systems, including cloud environments. With modern service-based software architectures, these solutions address the legacy challenges of connecting plant and systems, and in large organizations, modern OT data hubs can connect to hundreds of disconnected systems simultaneously, exposing millions of plant data streams to endpoints beyond the plant operations.
With the advancements in technology, new plant and enterprise network standards and designs have emerged which consider scalable industrial data access enabled in part by the new capabilities of modern operational data hubs. These modern industrial architectures and networks allow data at the OT device or system parameter level to be exposed and egressed at sub-millisecond resolutions if desired. Increasingly complex data structures (beyond time series) can be accessed alongside traditional process data, unlocking traditionally stranded data available from modern smart devices and plant systems. Below is a recently published architecture from LNS Research illustrating the use of operational data hubs and data lakes as a focal point for industrial data consolidation in modern industrial operations. LNS Article on Industrial Data Hubs In these architectures, legacy plant or enterprise historians are no longer required to broker data between the OT and IT domains as had been done in some digitalization efforts.
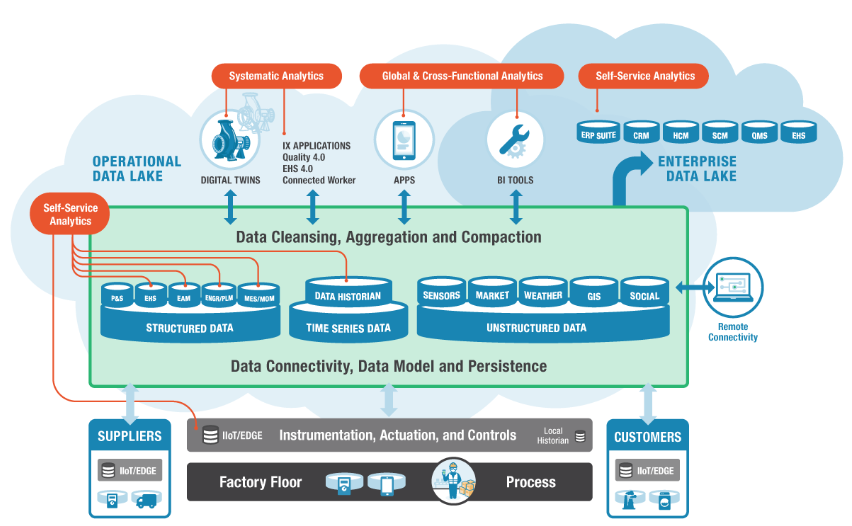
As Industry 4.0 has gained greater momentum and wider adoption, it has also had a notable impact on greenfield industrial builds. As organizations consider the digitalization of new assets during the capital phase of these projects, they want new industrial assets to be ‘born digital’ and completely aligned with corporate policy around data access and governance. The requirement is for data to be available to anyone, anytime, and at scale, aligning with the data transparency goals of Industry 4.0.
As organizations consider the digitalization of new assets during the capital phase of these projects, they want new industrial assets to be ‘born digital’ and completely aligned with corporate policy around data access and governance.
Historically, digital investments were never considered or included during detailed project designs. As a result, industrial organizations often made these investments later (or not at all), resulting in an ocean of stranded data and information inside of the operation itself. However, unlike manufacturing plants of the past, the design basis for modern facilities commonly includes important functional requirements associated with scalable OT device and systems-level connectivity, high-speed networks that bridge OT and IT domains, modern plant data systems, cloud system integration, and so on. With some of the technical and organizational barriers common in legacy plant operations removed, the capabilities afforded by new OT and IT can be leveraged to its full capability. It is a journey for each organization, but happily, we are seeing large-scale industrial digitalization accelerating.
Figure 1 "Goals of Industry 4.0 for Industrial Operations" Courtesy of Emerson
Figure 3 "New Data Architectures are Emerging for Industrial Plant Operators" Courtesy of LNS Research
For JWN Energy article: https://www.jwnenergy.com/article/2023/2/6/industrial-operations-reborn-digital/
For more information visit: Digital Transformation (spartancontrols.com)
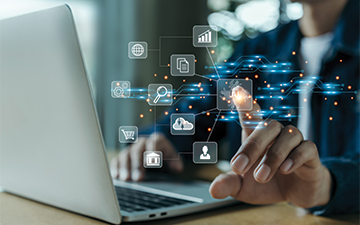