Author: Zeeshan Zia
The Purpose of Steam Traps
High-quality steam is essential for optimizing industrial operations. At Spartan, we are committed to delivering solutions that ensure reliability, efficiency, and long-term performance. Steam is generated at the boiler and distributed throughout the plant to transfer heat energy for various processes. As steam travels through the system, it condenses and accumulates in low points, requiring efficient removal to maintain optimal operation.
This is where steam traps come in. Strategically placed throughout the plant, steam traps effectively remove condensate, air, and other non-condensable gases, ensuring smooth and efficient steam flow.
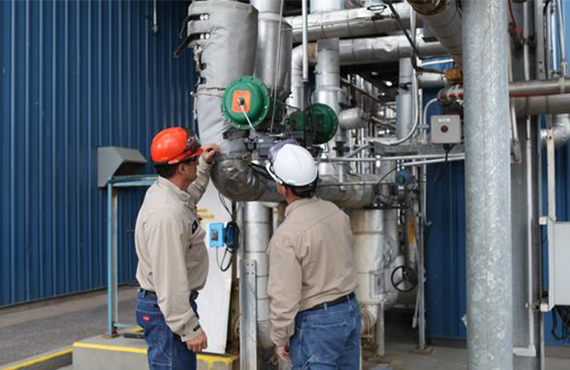
Proper steam trap operation is essential for avoiding several key issues, including:
- Equipment damage, unplanned maintenance, and unexpected failures
- Unnecessary risks to plant personnel
- Reduced productivity, lower throughput, and compromised product quality
- Higher fuel consumption, leading to increased operational costs
- Challenges in meeting environmental standards and sustainability goals
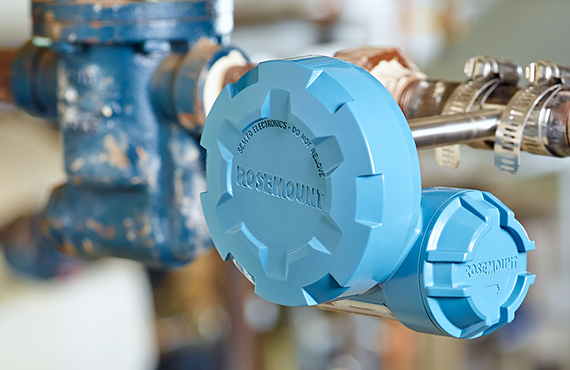
How to Optimize a Steam Trap Monitoring System
Empowering operators’ deeper insight into the health of steam traps and steam systems allows them to proactively manage maintenance, reduce failures, and enhance overall system performance. Advancements in measurement and transmitter technology now make continuous steam trap monitoring more cost-effective than ever.
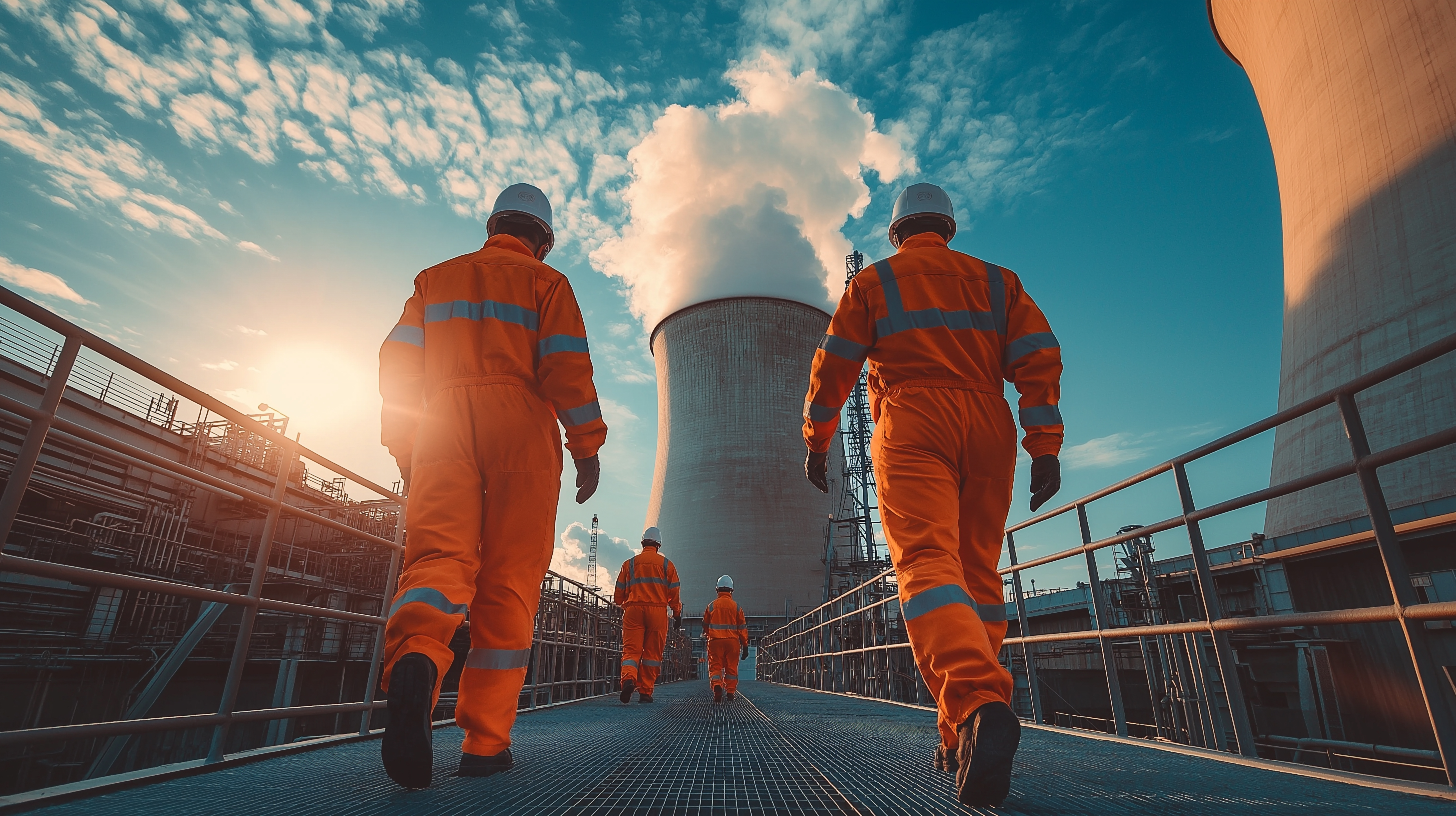
1. Proactive Maintenance
Real-time visibility allows operators to replace failing traps before they impact plant processes and efficiency.
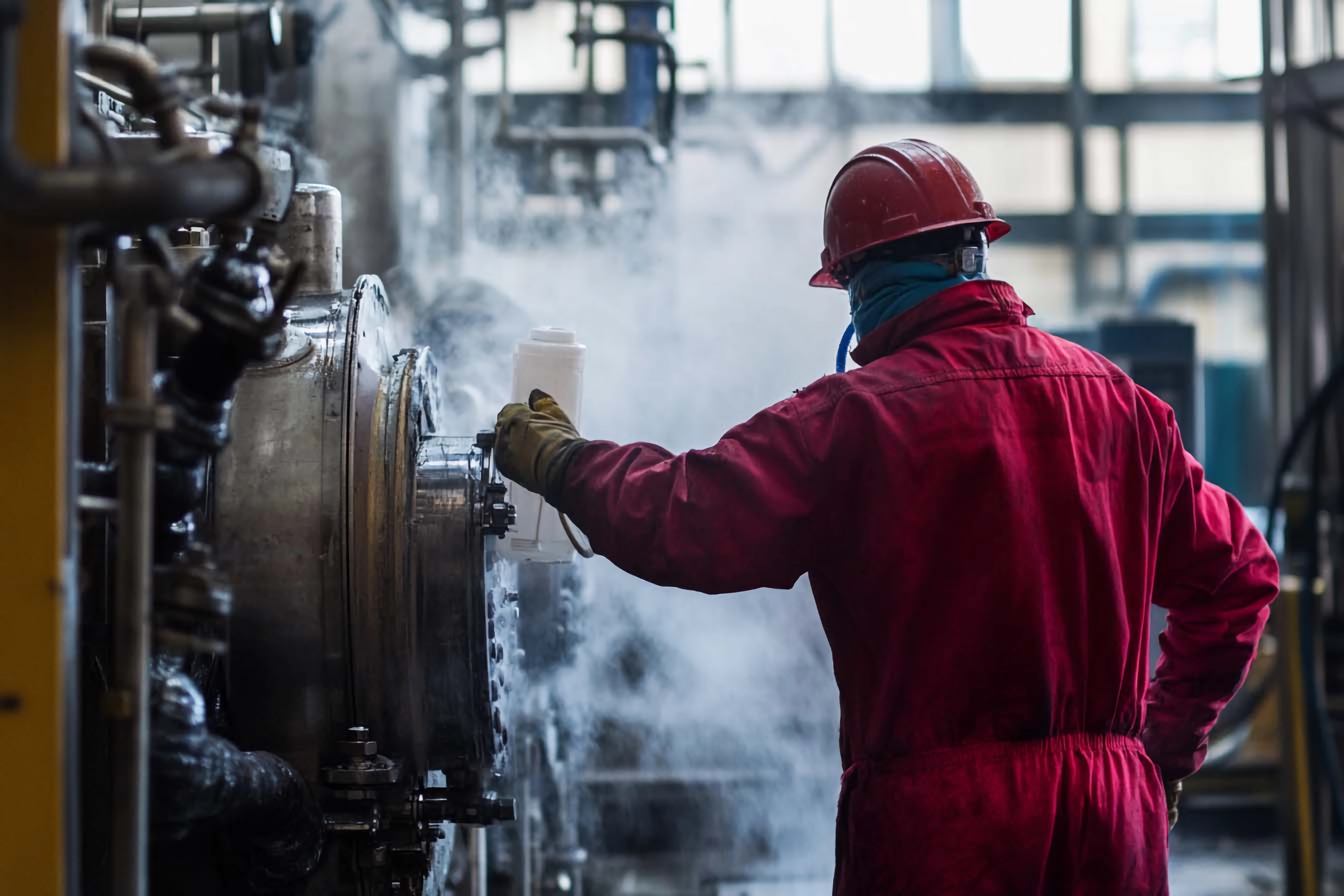
2. More Accurate Monitoring
Continuous monitoring provides a more comprehensive view of steam trap performance than periodic checks, which only capture a small snapshot of activity.
Wireless transmitters, which measure ultrasonic acoustic behavior and temperature, communicate directly with maintenance personnel via a wireless mesh network, ensuring reliable data transmission. With no need for extensive wiring, these transmitters are significantly more affordable than traditional wired instruments.
Empowering operators’ deeper insight into the health of steam traps and steam systems allows them to proactively manage maintenance, reduce failures, and enhance overall system performance.
Zeeshan Zia
A Four-Step Approach to Address Failed Steam Traps
To ensure long-term performance and reduce the impact of steam trap failures, adopt a structured, proactive approach:
- Perform a Regularly Scheduled Manual Steam Trap Survey: Include both temperature and ultrasonic testing to identify potential failure modes.
- Identify Critical Traps: Use methods such as steam loss calculation using Napier’s equation or Failure Modes and Effects Analysis (FMEA) to prioritize traps that are crucial to your process.
- Apply Real-Time Wireless Monitoring and Data Analysis: Focus on the high-risk traps identified in step two for continuous data collection and analysis.
- Take Action: Repair or replace failing steam traps before they cause significant operational issues.
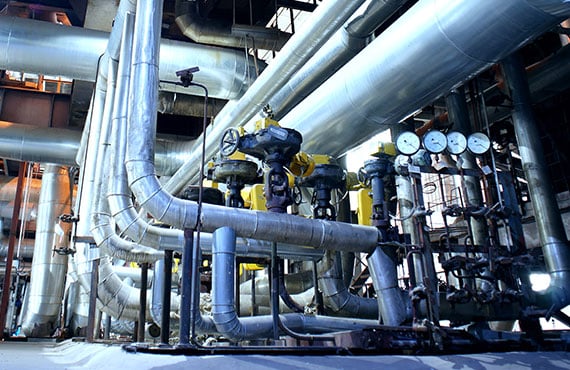
It’s essential for operations personnel to identify which steam traps are most critical to the process, assess the potential costs of failure, and understand how a malfunctioning trap can impact overall operations. One effective method for assessing risk is assigning a Risk Priority Number (RPN) during an FMEA evaluation.
This number helps to rank the severity of various potential issues by considering:
This number helps to rank the severity of various potential issues by considering:
- Occurrence: likelihood the failure will occur
- Detection: ability to detect a failure before it affects operations
- Severity: amount of harm or damage the failure mode may cause
- FMEA helps prioritize the most critical steam traps by calculating an RPN, guiding operators on where to focus their attention.
It’s essential for operations personnel to identify which steam traps are most critical to the process.
Zeeshan Zia
The Impact of Steam Trap Failures on Operations
Steam systems rely on properly functioning traps to remove condensate and air, maintaining system efficiency and protecting equipment. When steam traps fail, the consequences can be far-reaching, affecting energy consumption, throughput, equipment lifespan, and even safety.
Traditionally, steam trap condition is assessed through third-party audits, which involve measuring ultrasonic acoustic behavior and temperature to detect failures. While these audits provide useful data, they have significant limitations: they offer only a snapshot of trap performance and are highly dependent on the technician's expertise. Moreover, without continuous monitoring, failed traps can go undetected for extended periods between audits, leading to costly inefficiencies and potential system failures.
Traditionally, steam trap condition is assessed through third-party audits, which involve measuring ultrasonic acoustic behavior and temperature to detect failures. While these audits provide useful data, they have significant limitations: they offer only a snapshot of trap performance and are highly dependent on the technician's expertise. Moreover, without continuous monitoring, failed traps can go undetected for extended periods between audits, leading to costly inefficiencies and potential system failures.
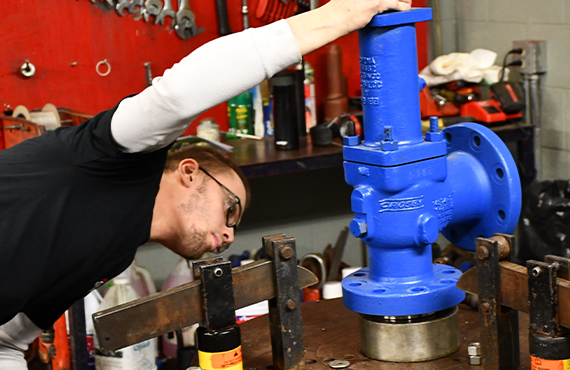
Why Continuous Monitoring is a Game-Change
With wireless transmitter technology, continuous, real-time monitoring of steam traps is now accessible and cost-effective. This solution provides repeatable, accurate, and reliable monitoring, particularly for high-value steam traps that have the most significant impact on plant operations. By implementing continuous monitoring, operators can identify and address steam trap failures quickly, yielding substantial energy savings, increased operational efficiency, and fewer unplanned maintenance events.
Investing in a continuous monitoring system for your steam traps will not only provide quick returns on energy savings but also deliver long-term benefits by improving system performance, extending equipment life, and reducing overall maintenance costs.
Investing in a continuous monitoring system for your steam traps will not only provide quick returns on energy savings but also deliver long-term benefits by improving system performance, extending equipment life, and reducing overall maintenance costs.